The Kit consists of axle brackets, frame brackets, bushings for the axle end, Ballistic JJ's for the frame end, a heim for where the upper arm meets the lower, a saddle for the heim, 2" x 1/4" DOM links, and all the necessary hardware.
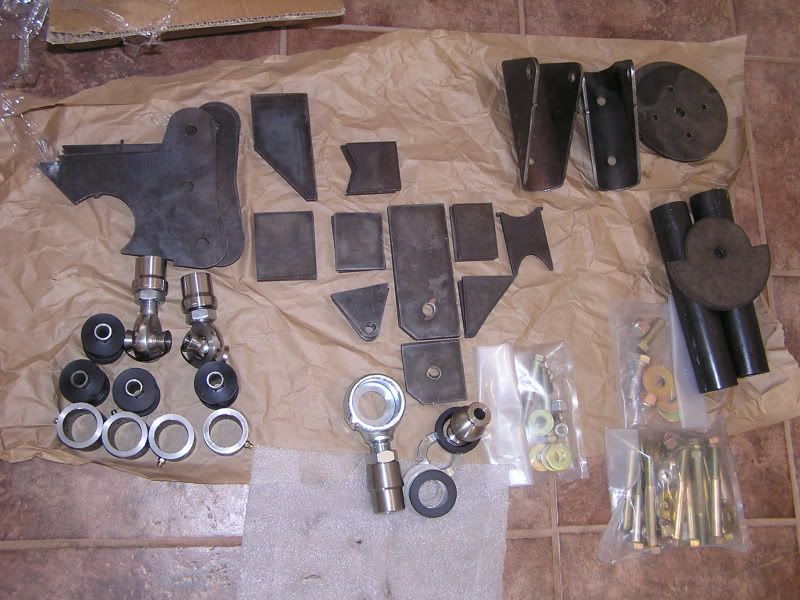
There was a little fit and finish issue with the Ballisitic joints in that there were several burrs inside the housing that shouldn't be there. A little die grinding fixed that:
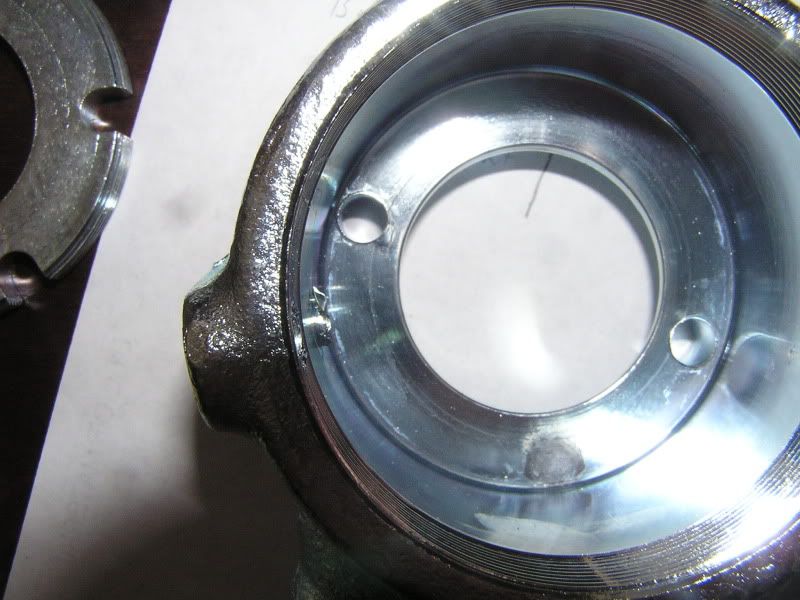
I am using a friends garage because he has a nice plasma cutter and welder. He lives about 10 miles from home, but he has space to leave my bronco inside for a couple weekends. Saturday around noon had the axle out of the bronco:
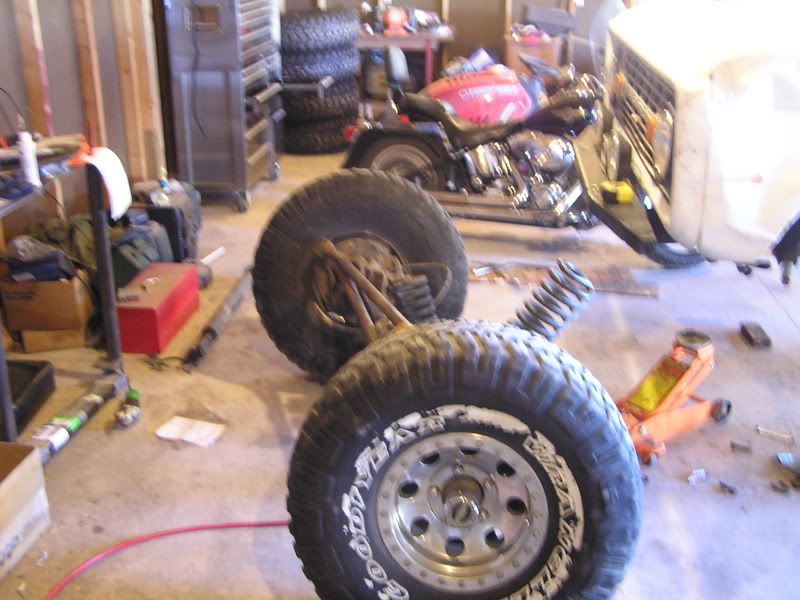
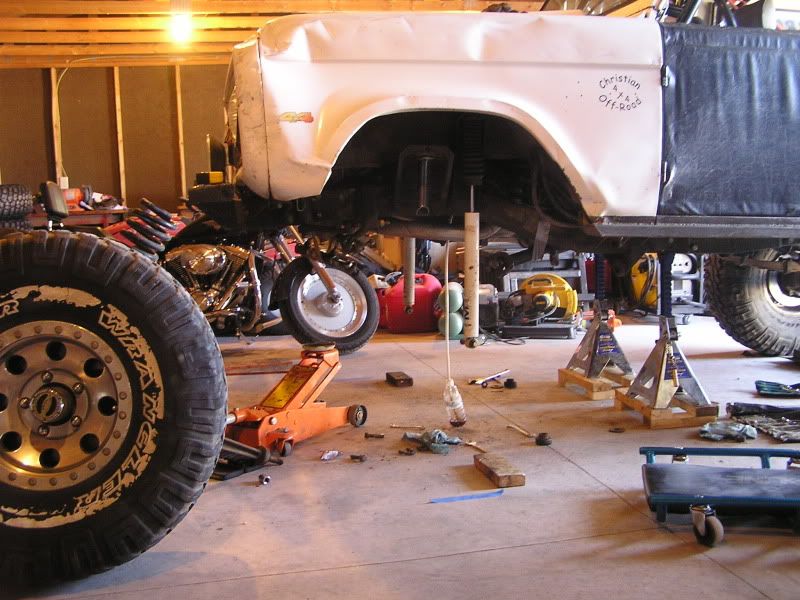
I then began cutting off the stock axle and frame brackets with the plasma. That took me a few hours and I still have some cleanup to do.
I wasn't sure how the frame brackets went together. My phone call hadn't been returned by the shop so I was kinda dead in the water. I decided to fit up the axle brackets and noticed they were made for a D60 tube, which is 1/2" larger than mine! :shock: So I took a break from my bronco and helped a friend install a 2" lift on his 2010 tacoma.
Got a call from the shop that evening and he walked me thru the design of the frame bracket. Just some of the plates didn't fit like they should have and that's where the confusion stemmed. He also apologized for sending me the wrong axle brackets and was sending a local friend of mine the file to cut the correct ones on his plasma table the next day. I went to Big R and got a few supplies for the following day and then called it a day.
Sunday morning I got started early again and used some of the hardware from Big R to assemble my joints. The PVC coupling worked great!
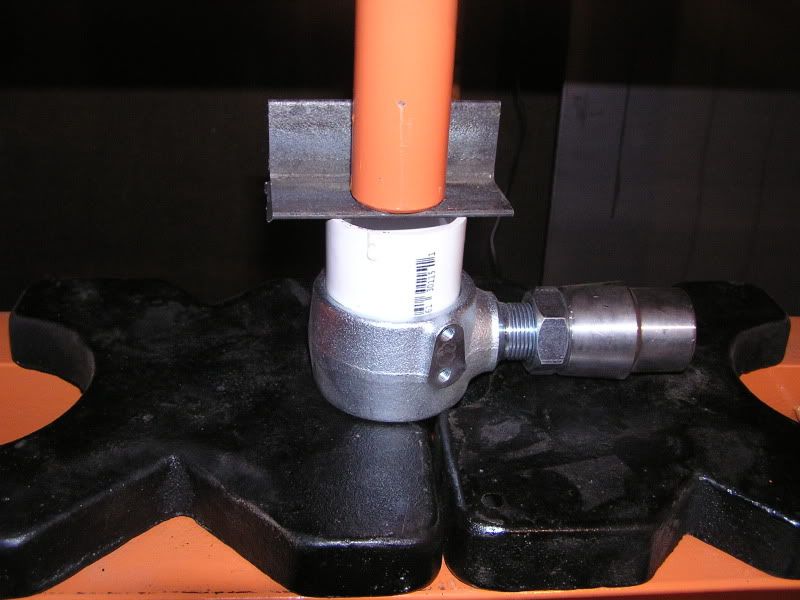
I had help from my cousin on Sunday and he's got much prettier welds than I do, so I had him build a frame bracket:
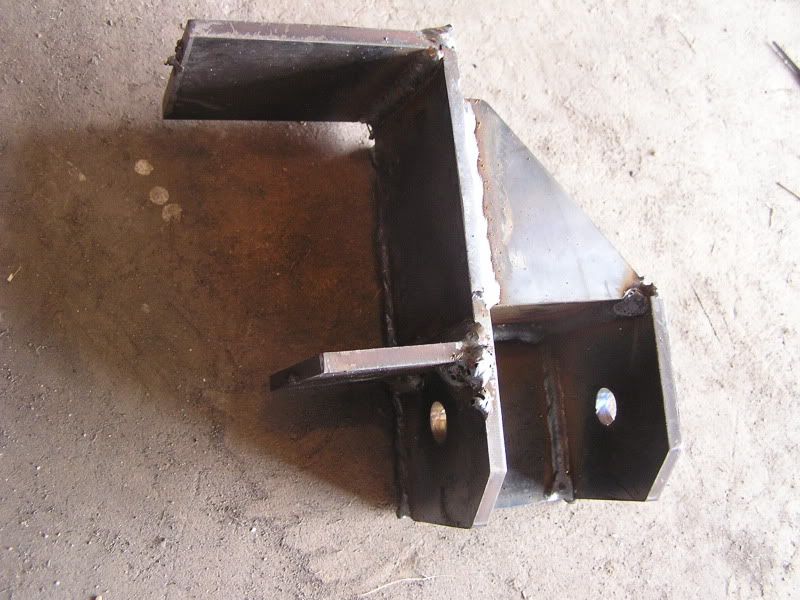
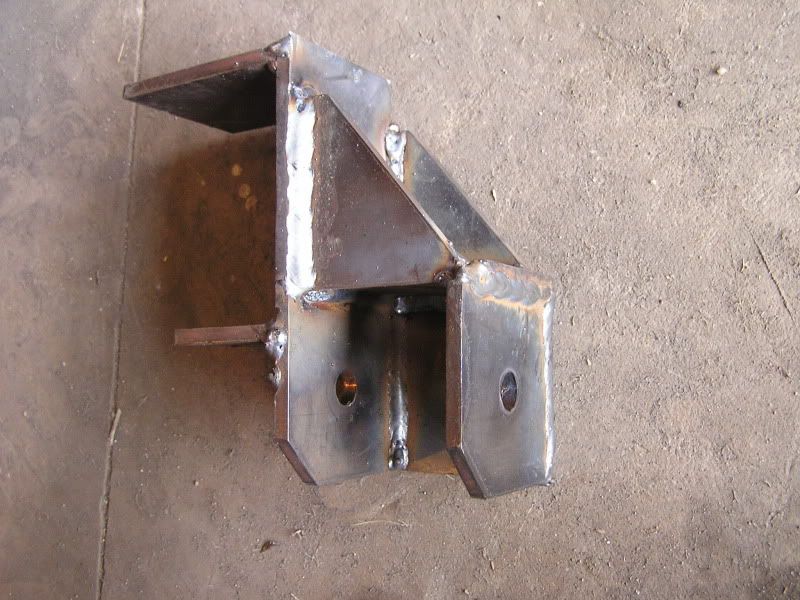
After this, we headed to my friends house to get the correct axle brackets cut. This cost me 5+hrs of work, but had to have it.
When we returned, my cousin welded the new frame bracket in place as far back as possible.
Front side:
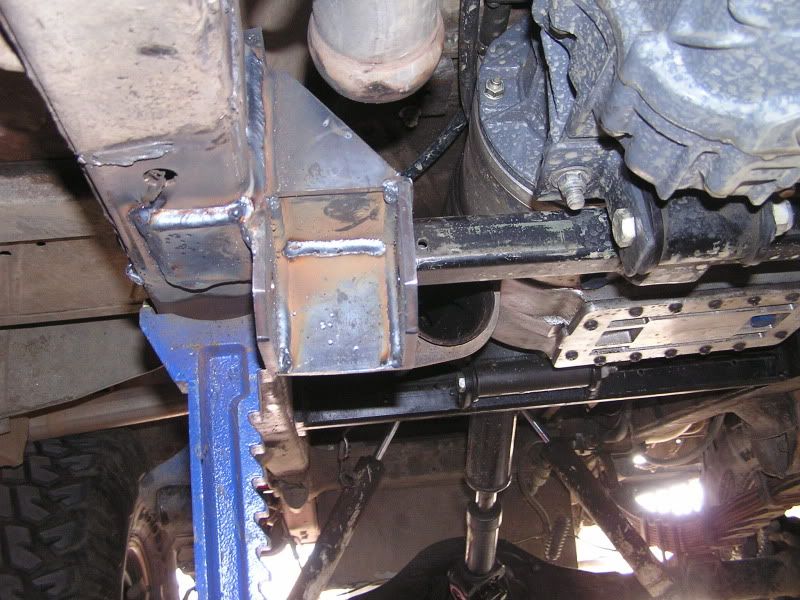
Back side:
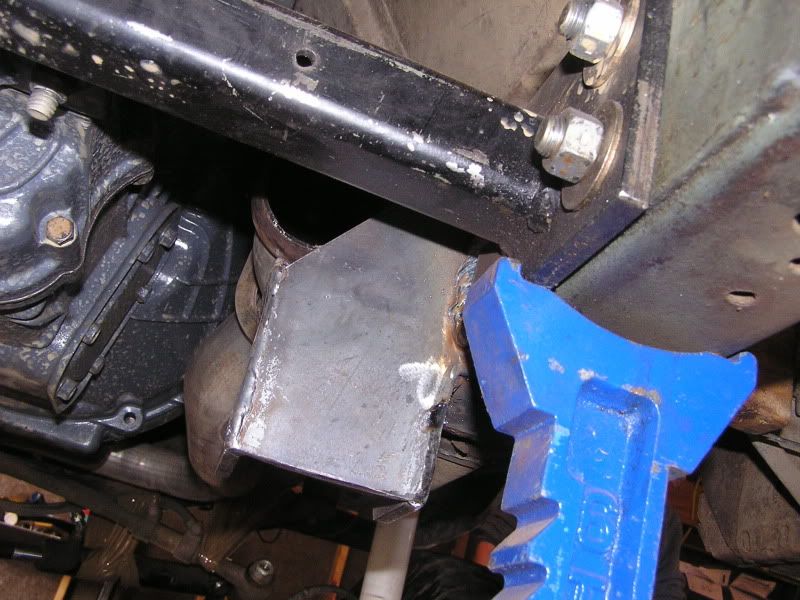
He also welded the drivers side together for me, but ran out of time and had to go home. Leaving me to weld the drivers side bracket in myself.
Not pretty, but I think it stuck:
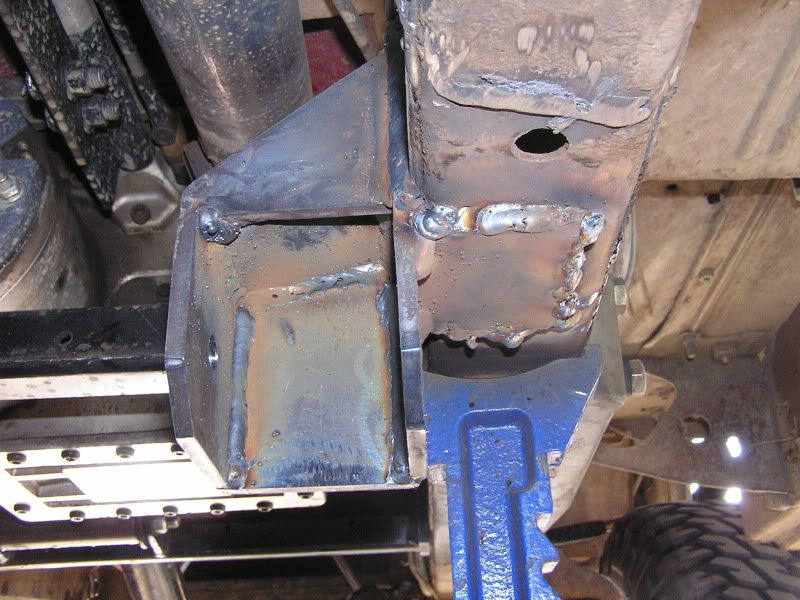
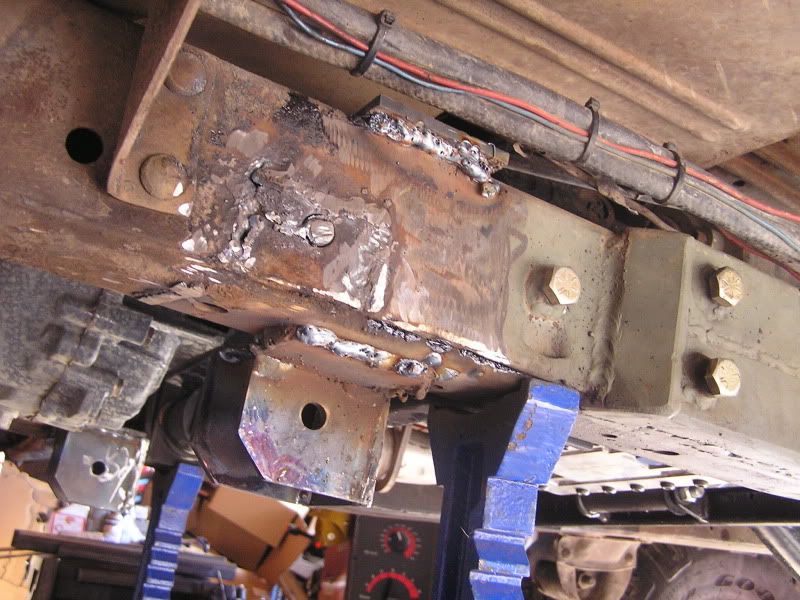
It was time to move onto the axle brackets. After some cleanup I started putting them together and had some of my best welds ever!
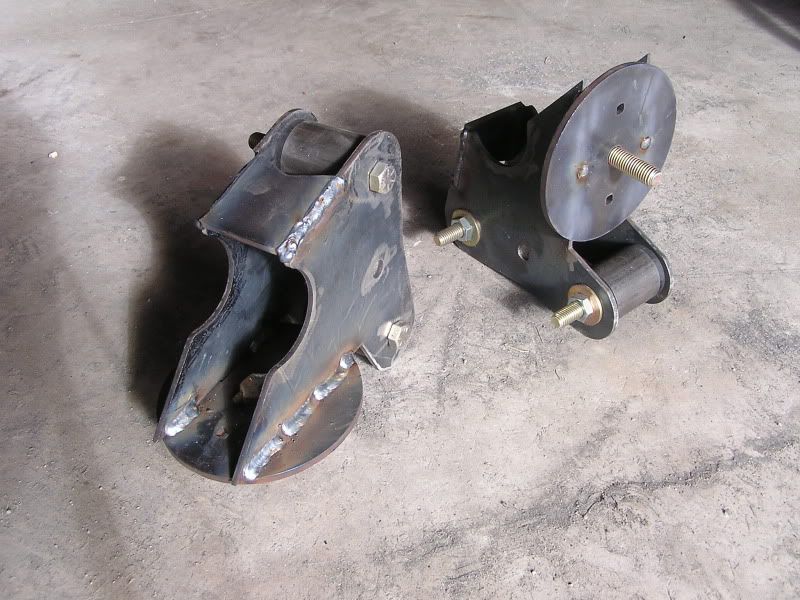
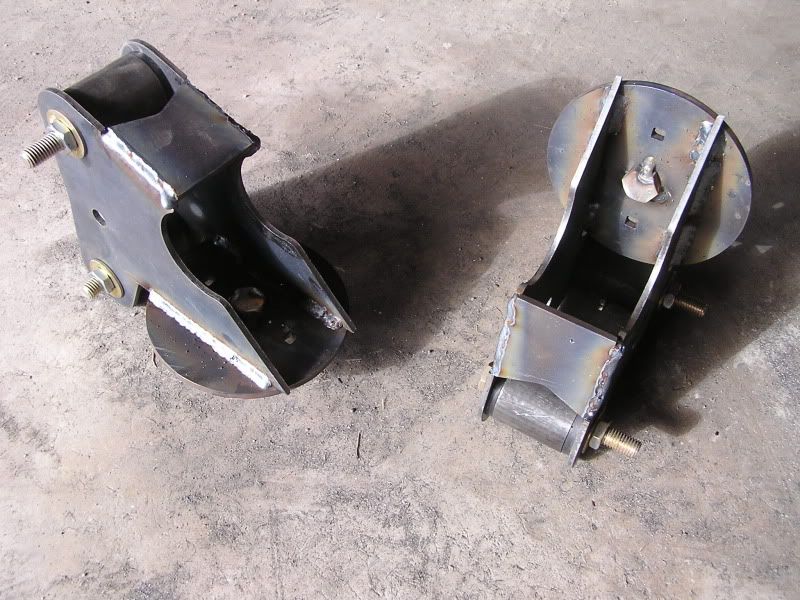
Got them tacked onto the axle and rolled the axle in place to verify it will all work. Once I was happy with the layout, I welded them in solid to the axle. these are some of the worst looking welds I had, but again, I think they are welded solid:
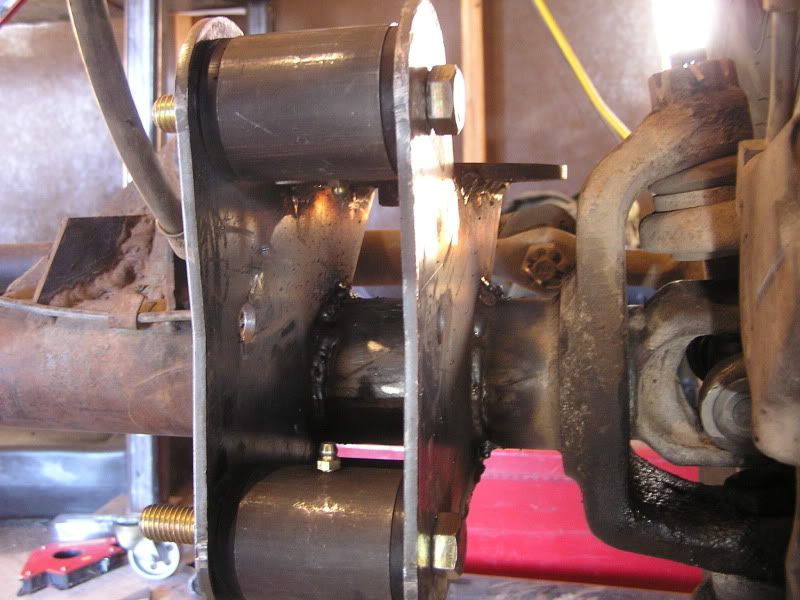
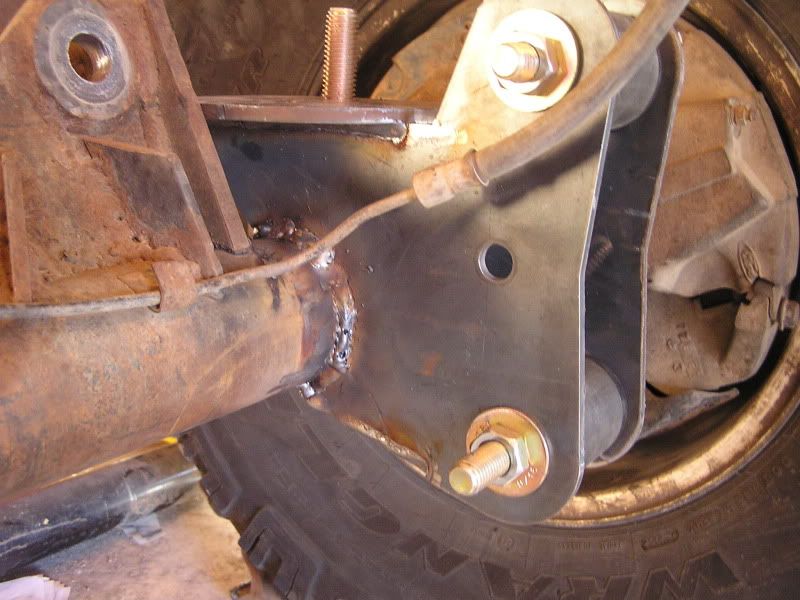

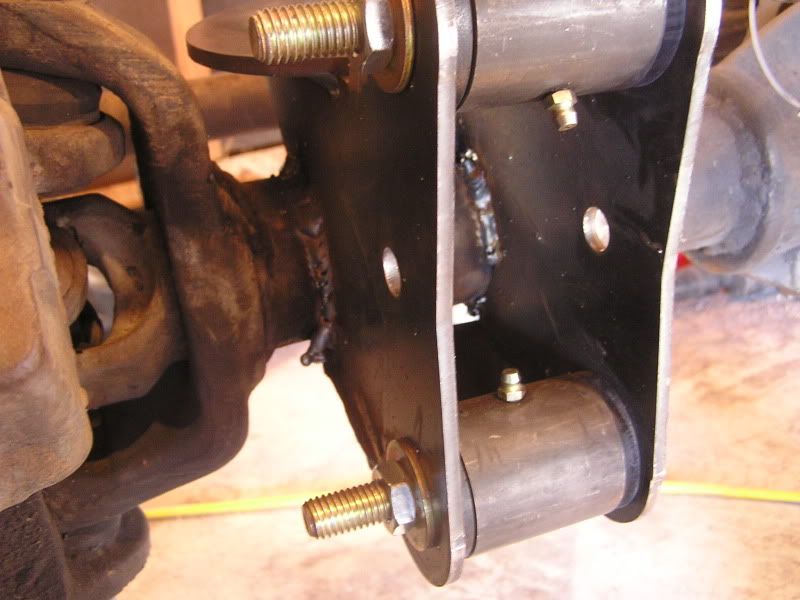
I again rolled the axle back under the bronco and started measuring for lower links. The lower arms meet the bushings at a bit of an angle, so the


Happy with my progress, but a little disappointed that having the wrong axle brackets cost some hours. But why should this project go smooth and be any different than any of my others...??
Stay tuned next week as I am hoping to take one day and finish it, complete with paint and suspension flex pictures!
J.D.